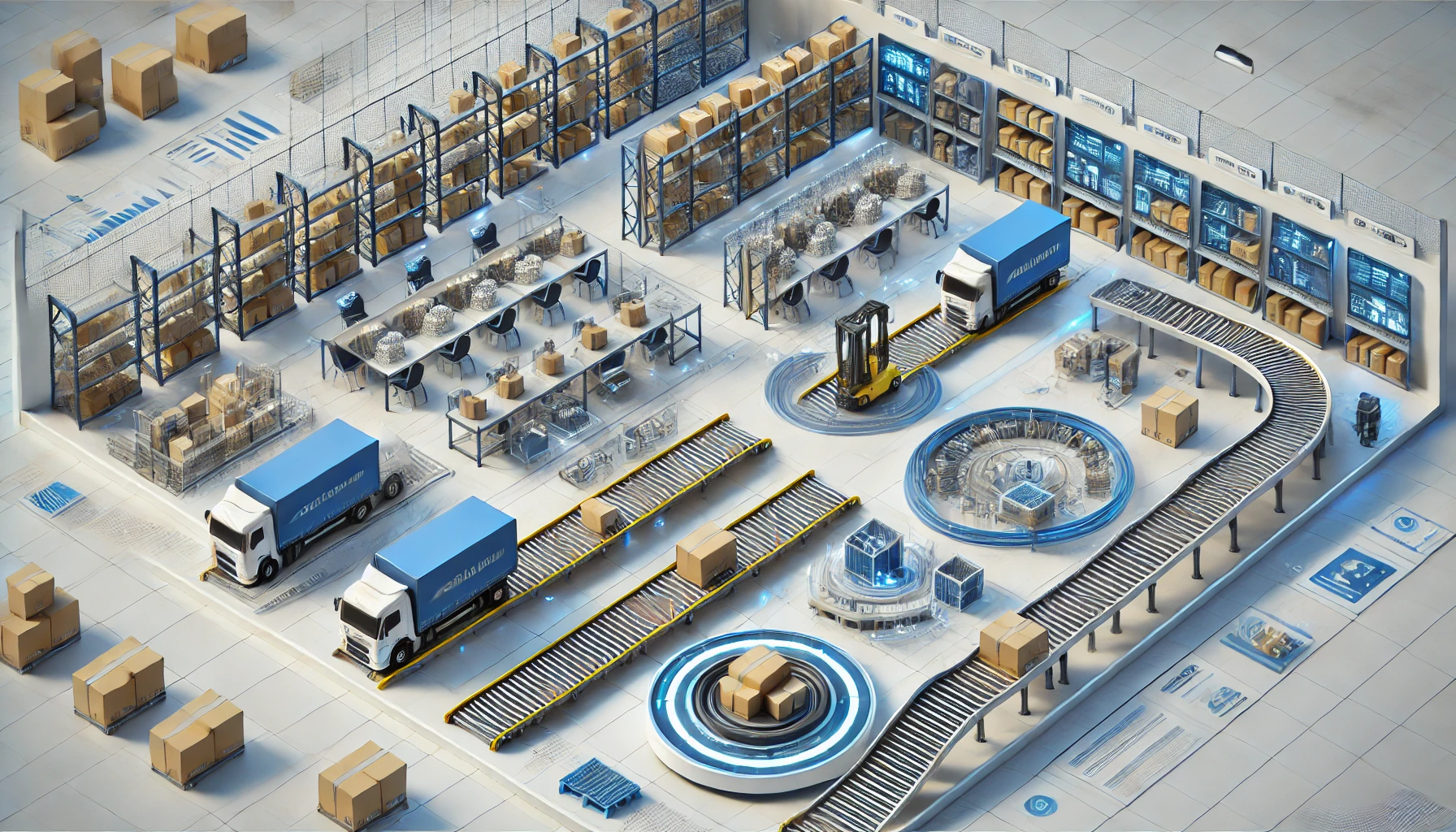
In today’s fast-paced logistics environment, efficient inventory management is more than just a back-end operation—it’s a competitive edge. For warehouses, fulfillment centers, and 3PL providers, the right inventory method can influence waste reduction, delivery accuracy, and profitability.
Two inventory systems dominate logistics today: FIFO (First In, First Out) and LIFO (Last In, First Out). Each offers strategic advantages depending on the products you handle, your operational model, and your market conditions. This article breaks down both methods to help you choose the right one for your fulfillment needs.
Understanding FIFO and LIFO in Warehouse Logistics
First In, First Out (FIFO) means older stock is sold or used before newer inventory. It’s a strategy often favored in:
Food and pharmaceutical logistics
Micro fulfillment centers
Inventory requiring regulatory compliance (e.g. FEFO)
FIFO supports traceability and stock freshness, making it ideal for high-turnover, perishable goods.
What is LIFO?
Last In, First Out (LIFO) means the most recently added inventory is used first. This strategy is commonly seen in:
Non-perishable product warehouses
Financial environments affected by inflation
U.S.-based companies optimizing tax outcomes
LIFO can reduce taxable income during inflation by matching recent costs with sales prices.
FIFO in Micro Fulfillment Centers – When Freshness is Critical
Advantages of FIFO:
Reduced waste from expired stock
Better stock rotation, especially in high-volume categories
Regulatory compliance for food, health, and pharmaceutical products
More accurate cost tracking in rapidly moving inventory systems
Disadvantages of FIFO:
Can lead to lower profit margins during inflation
Requires advanced WMS to track older inventory precisely
Less relevant for non-perishable goods
LIFO in 3PL Operations – When Cost Control Comes First
Advantages of LIFO:
Tax savings in inflation-heavy markets
Operational simplicity for certain SKUs
Inventory cost alignment with volatile markets
Disadvantages of LIFO:
Customer satisfaction risk in D2C environments
Regulatory limitations: not permitted under IFRS (outside U.S.)
FIFO vs LIFO – How to Choose the Right Strategy
When selecting between FIFO and LIFO, consider:
Criteria | FIFO | LIFO |
---|---|---|
Best for | Perishables, health products | Non-perishables, bulk items |
Financial advantage | Accurate cost reporting | Lower taxable income |
Regulatory acceptance | Global | U.S. only |
Risk level | Low expiration risk | High obsolescence risk |
Use FIFO if your logistics model requires freshness and traceability.
Use LIFO if your inventory costs are volatile and your operation is U.S.-based.
CONCLUSION
In the evolving world of logistics, inventory strategy is not one-size-fits-all. Both FIFO and LIFO can bring significant operational and financial benefits—but only if matched to the right product type and fulfillment model.
Businesses that take the time to evaluate their supply chain goals and customer expectations can use these methods to reduce waste, improve delivery accuracy, and gain a competitive edge in the logistics ecosystem.
Need help implementing the right inventory strategy for your LATAM operations? Kiki Latam offers customized 3PL logistics and fulfillment models—built for your growth, product type, and market conditions.