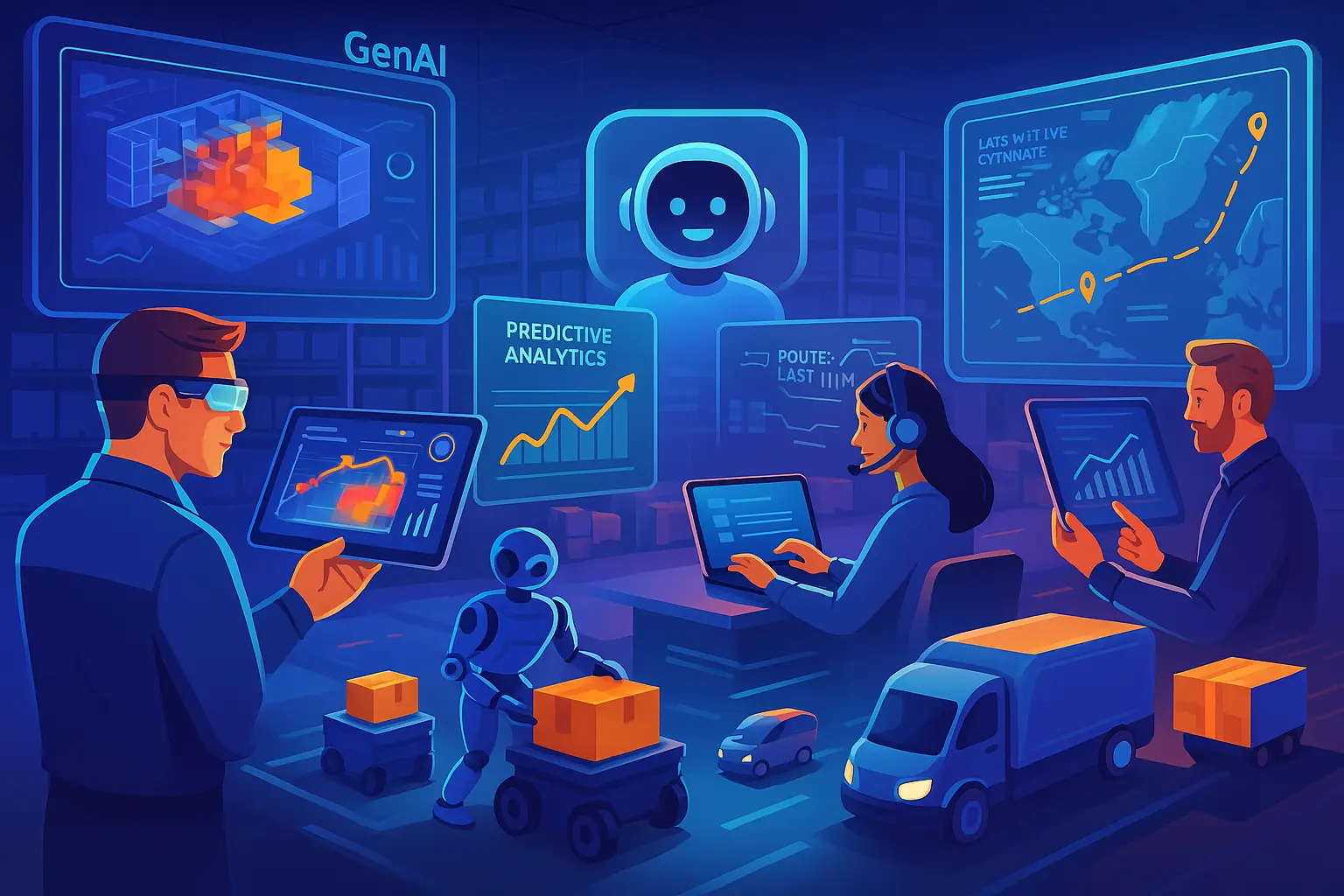
The logistics industry is undergoing a technological leap, and Generative AI (GenAI) is leading the charge. No longer a future promise, GenAI is actively transforming how businesses manage aftermarket operations, field services, and fulfillment workflows.
From reducing service costs to boosting technician productivity and automating order routing, GenAI is introducing a new era of logistics efficiency. As companies race to digitize, those who successfully scale AI are pulling ahead—with tangible results.
Kiki Latam is among those innovators, integrating GenAI into its operations to support smarter logistics, personalized service, and scalable fulfillment across Latin America.
GenAI in Logistics: From Concept to Execution
What Is GenAI Doing in Logistics?
Generative AI refers to AI systems that not only analyze data but generate content, decisions, and insights dynamically. In logistics, this means:
- Predictive Inventory Planning: AI forecasts spare parts demand, preventing shortages and delays.
- Service Automation: Real-time diagnostic scripts and troubleshooting guides help technicians resolve issues faster.
- Customer Interaction: GenAI-trained support tools offer faster, personalized service, improving SLA compliance.
According to Capgemini, over 40% of supply chain executives have already implemented GenAI in some capacity, especially in aftermarket and field operations.
Scaling GenAI Across Fulfillment & Field Services
The Three Building Blocks of Success
Despite strong interest, many companies fail to move beyond pilot programs. McKinsey & Company identifies three pillars that define successful scaling:
- Unified Data Infrastructure
Integrate fragmented datasets across warehouses, transportation systems, and customer platforms to feed GenAI models. - Human + AI Collaboration
Empower frontline workers with intuitive AI interfaces that assist, rather than replace, human decision-making. - Modular Implementation
Focus first on high-impact use cases like order processing, reverse logistics, and field dispatch to prove value quickly.
These steps can reduce service costs by up to 30%, while improving both agility and customer experience.
GenAI’s Real Impact on Logistics & Fulfillment
Automated Fulfillment and Dynamic Routing
- NLP-Powered Workflows: Natural Language Processing (NLP) enables auto-processing of shipping instructions and inventory updates.
- Real-Time Routing: GenAI models adapt to road conditions and traffic, optimizing ETAs in last-mile delivery.
- Inventory Heatmaps: AI predicts where stock should be positioned, based on historical demand and seasonal patterns.
This translates into faster deliveries, fewer stockouts, and smarter resource allocation.
Field Service Optimization
- First-Time Fix Rates: GenAI-driven diagnostic tools help technicians resolve issues on the first visit.
- Predictive Maintenance: IoT sensors paired with GenAI forecast when delivery vehicles or warehouse equipment need attention.
- Knowledge Base Creation: AI builds dynamic support libraries for service agents, reducing response times.
These improvements increase uptime, reduce operational risk, and elevate customer trust.
Kiki Latam: Driving GenAI Logistics Innovation in LATAM
Kiki Latam is actively investing in GenAI-powered logistics capabilities to support its clients across Latin America. Our focus is on enhancing visibility, automation, and cost efficiency in both fulfillment and service delivery.
What We’re Building:
- AI-Assisted Inventory Management: Automated restocking and demand planning across regional fulfillment hubs.
- GenAI-Enhanced Customer Support: AI-generated service scripts improve response times and resolution rates.
- Predictive Maintenance for Logistics Assets: Real-time monitoring of vehicles and warehouse equipment extends lifespan and ensures uptime.
- Smart Order Routing: AI models dynamically assign carriers based on availability, cost, and delivery urgency.
By leading the implementation of GenAI in the region, Kiki Latam is shaping a new standard for intelligent logistics and service operations.
Why Generative AI Is a Competitive Advantage
The benefits of GenAI aren’t theoretical—they’re measurable:
- Up to 50% reduction in service wait times
- Improved accuracy in order fulfillment and routing
- Lower field service costs through automation and planning
- Stronger customer retention through personalized support
For businesses operating in complex geographies like Mexico, Colombia, and Peru, GenAI offers the agility and intelligence needed to scale effectively.
Generative AI is not just a trend—it’s a strategic differentiator. From personalized customer support to automated fulfillment and field optimization, GenAI is revolutionizing logistics across the board.
But success isn’t about using GenAI—it’s about scaling it with purpose.
At Kiki Latam, we’re helping companies turn AI innovation into operational performance. Whether you’re navigating fulfillment challenges or upgrading service operations, we provide the tools, infrastructure, and intelligence to make AI work for you.
👉 Book a consultation with our GenAI logistics team today and take the next step toward smarter, faster, and more scalable logistics across LATAM.